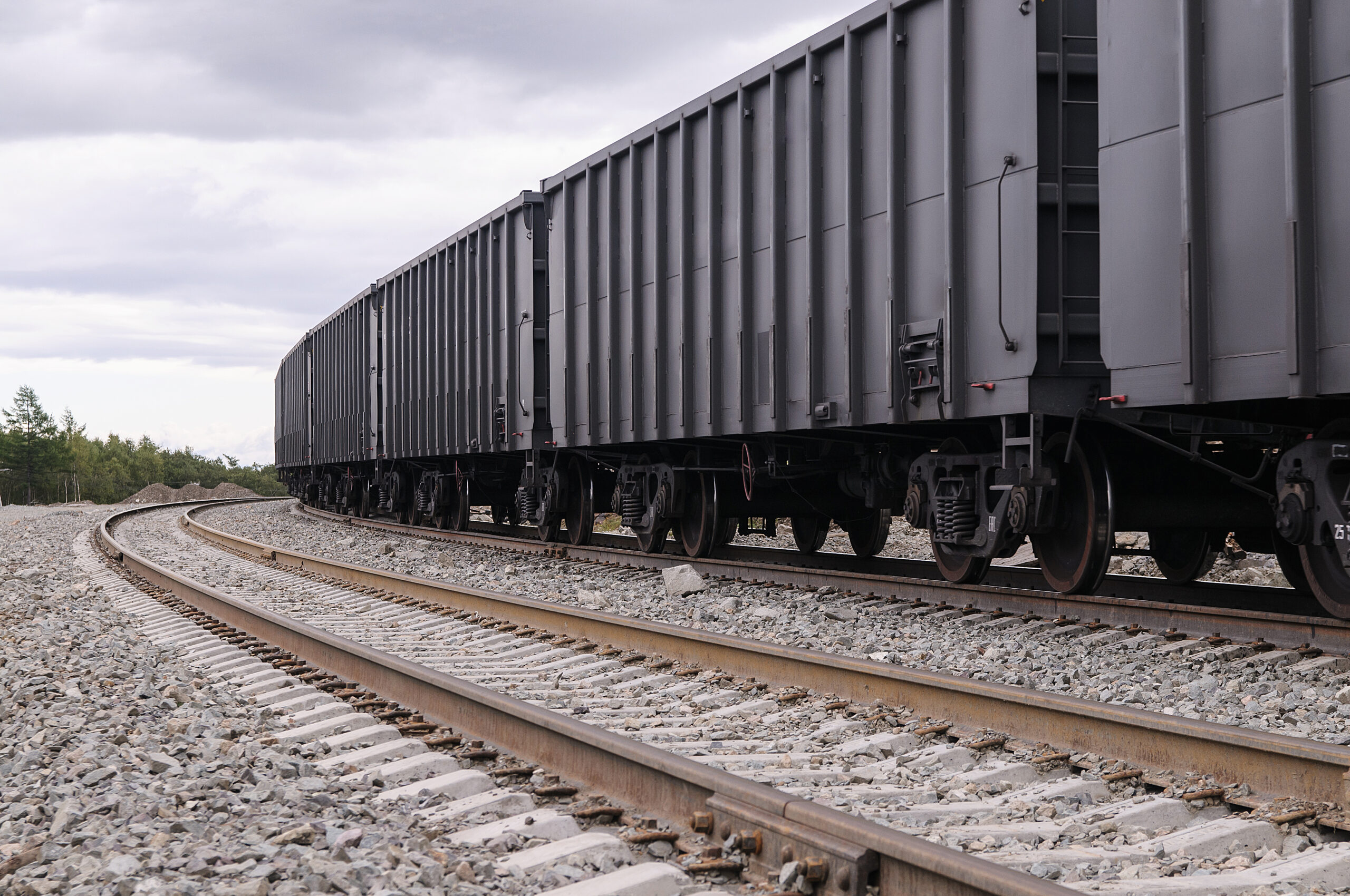
Tetra Tech’s three-dimensional track assessment system (3DTAS)—a RailAI® data collection subsystem—collects track surface, tie, and fastener elevation data with 0.35-millimeter (mm) (.014-inch [in.]) detail accuracy for precise real-time asset location, inventory, and assessment. Defect alerts based on customer business rules are issued in real time.
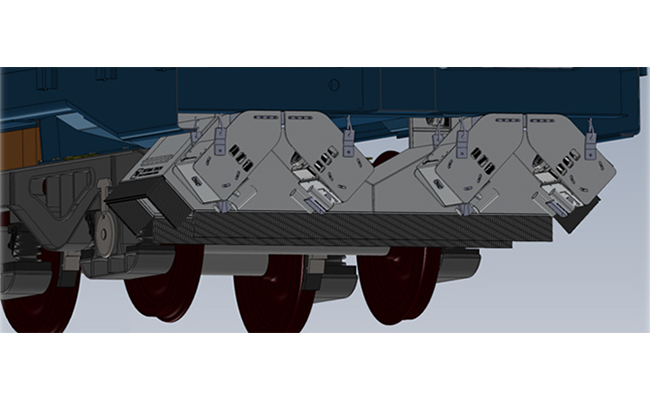
3DTAS is a fully integrated and turnkey track assessment system that collects full‑width, high‑resolution, 3D track surface profile data at track speed.
The system is able to assess and report rail, tie, and fastener physical parameters and tie condition parameters. 3DTAS accurately assesses both wood and concrete tie condition. All data is precisely georeferenced to allow individual tie location, repeat run comparisons, and change detection over time.
3DTAS comprises two high‑speed, 3D laser sensor enclosures; a 3D sensor controller; a power controller; an integrated data acquisition system; a local data storage array; a Desktop Management Interface (DMI) encoder; and all required interface cables. A patented, permanent rigid safety shroud is mounted beneath the test car around the 3D sensor enclosures to provide ambient light shielding and ocular hazard protection.

Real-time processed results from 3DTAS are stored on the onboard, large, network-attached storage (NAS) disk system.
3DTAS collects detailed track surface elevation data, which is used to pinpoint, inventory, and assess individual track assets in real time. As features of interest or defects—as defined by the customer’s business rules—are identified during surveys, 3DTAS produces event messages that are sent to the telemetry system for transmission to the customer’s back office or system as desired. Real-time results are precisely geospatially referenced and archived onto the onboard NAS.
3DTAS interacts with the onboard autonomous health monitoring and control system (HMCS) during data collection activities. Based on survey conditions (e.g., climate, sensor window obscurity, and power), the HMCS and RailAI system autonomously start and stop data collection based on train movement.
3DTAS Provides the Following Extensive Railroad Infrastructure Measurement and Assessment Data
-
Wood and Concrete Tie Inventory and Assessment
Accurate positional referencing combined with objective tie and fastening system analysis is the foundation of comprehensive asset management and the basis for development of cost effective operating expense and capital maintenance plan decisions.
3DTAS provides objective, accurate, and repeatable tie condition assessments; detailed physical measurements; and comprehensive fastening system evaluations. Tie condition scoring is based on tie surface distresses (e.g., cracking, breaks, and surface wear) and either industry-established default thresholds or client-customizable thresholds. Tie and fastening system physical parameters are also determined (e.g., length, width, skew, and height) with 0.04-in. accuracy. These assessments and component measurements provide the inputs to client‑defined track condition rules, which trigger real‑time exceptions and alerts.
-
Plate Cut, Rail Seat Abrasion, and Pad Wear Assessment
Tie surface wear impacts fastening system effectiveness and is a fundamental tie condition parameter. The submillimeter elevation measurement capabilities of the 3DTAS enables determination of accurate rail plate, rail base to tie surface measurements. Accurate assessments of tie surface, rail seat, pad, or insulator wear allow the precise selection of the most cost‑effective maintenance and rehabilitation strategies. Reliable repeat run‑over‑run comparisons allow modeling of component wear rates and the development of seat wear maintenance planning and mitigation. The combination of 3DTAS and geometry system measurements permit analyzing of the impact of rail pad wear and rail seat abrasion on fastener toe loads.
-
Fastener and Anchor Condition Assessment and Inventory
Tie plate inventory, spiking patterns, and loose and missing fasteners are detected and inventoried. Exceptions are reported in real time based on client-defined business rules for allowable parameter limits. Anchor type, tie edge offset, skew angles, and boxing patterns are recorded. Accurate run-over-run referencing and anchor inventory comparisons allow monitoring anchor movement and rail stress changes.
-
Tie Finger Printing and Precise Georeferencing
3DTAS detects and assesses the condition of each tie and measures its physical parameters. The physical and composite condition measures are used to characterize the tie to produce a unique “fingerprint,” which, when combined with accurate geospatial referencing, allows the accurate location of that specific tie in the field by personnel for inspection or marking. These unique fingerprints are used in comparing tie condition data run‑over‑run.
-
Railhead Defect Assessment
Early detection of railhead defects and cracking can enable preemptive maintenance intervention and rail grinding program optimization to achieve maximum life of the rail. The 3DTAS can identify crushed heads, corrugation, and battered joints that can cause significant dynamic loads imparted into the rail bed on tangent track. These dynamic loads can be extreme in curved track.
-
RailTurnout and Crossing Assessment and Inventory
Turnouts and crossings are subject to large repetitive forces accelerating asset wear. Accurate 3D measurements of turnout and crossing components allow noncontact inventory and assessment during normal test car movements in revenue service. Measurements can include inspection of ballast, ties, fasteners, switch gaps, check rail, and frog height and gaps. Estimates of switch area rail wear are also possible.