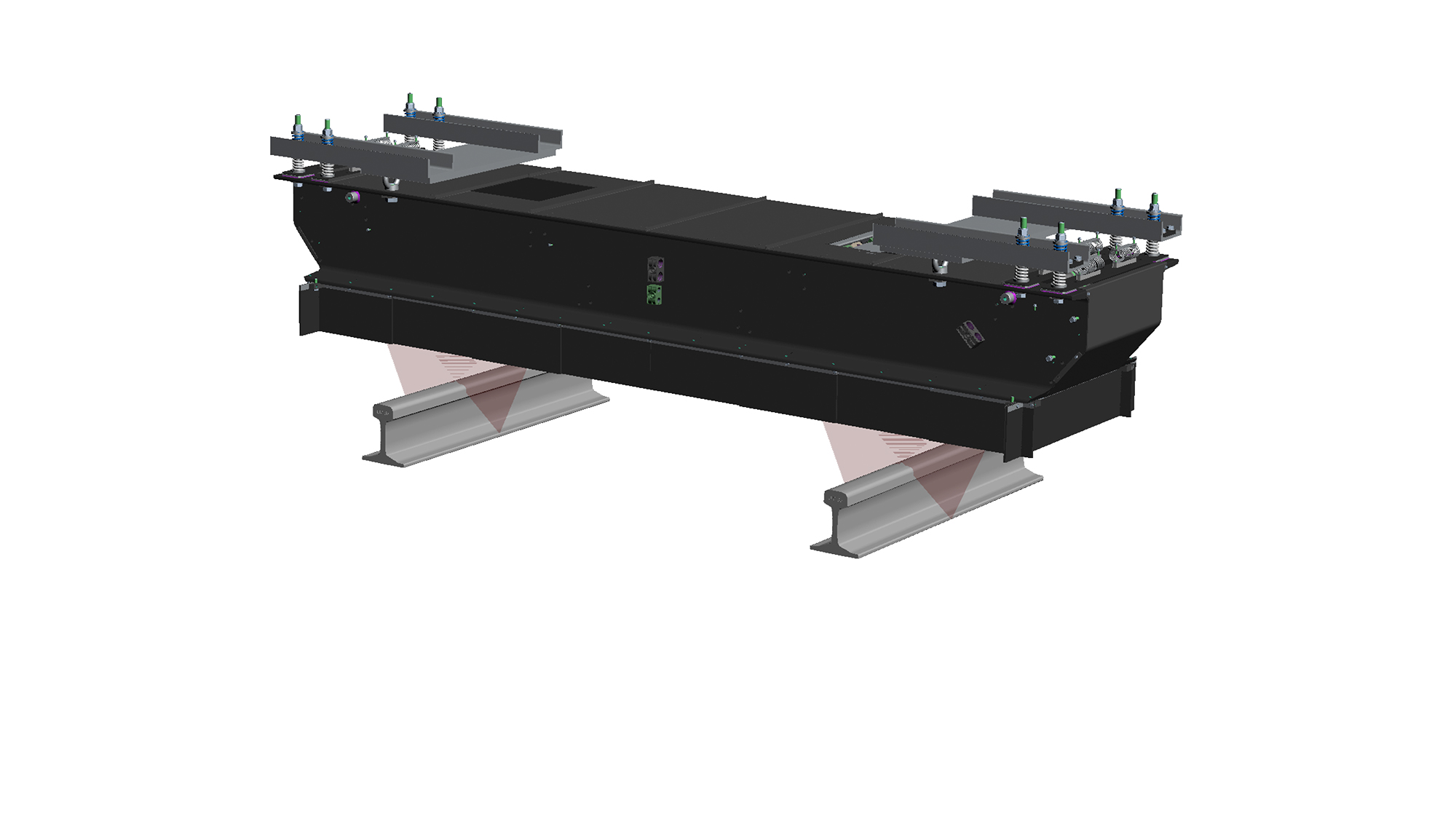
Tetra Tech fully integrates a highly accurate and reliable DMA Track Geometry Measurement System (TGMS) into its RailAI® boxcars. Tetra Tech also can integrate with systems or upgrade geometry cars from other suppliers by adding its RailAI track assessment systems.
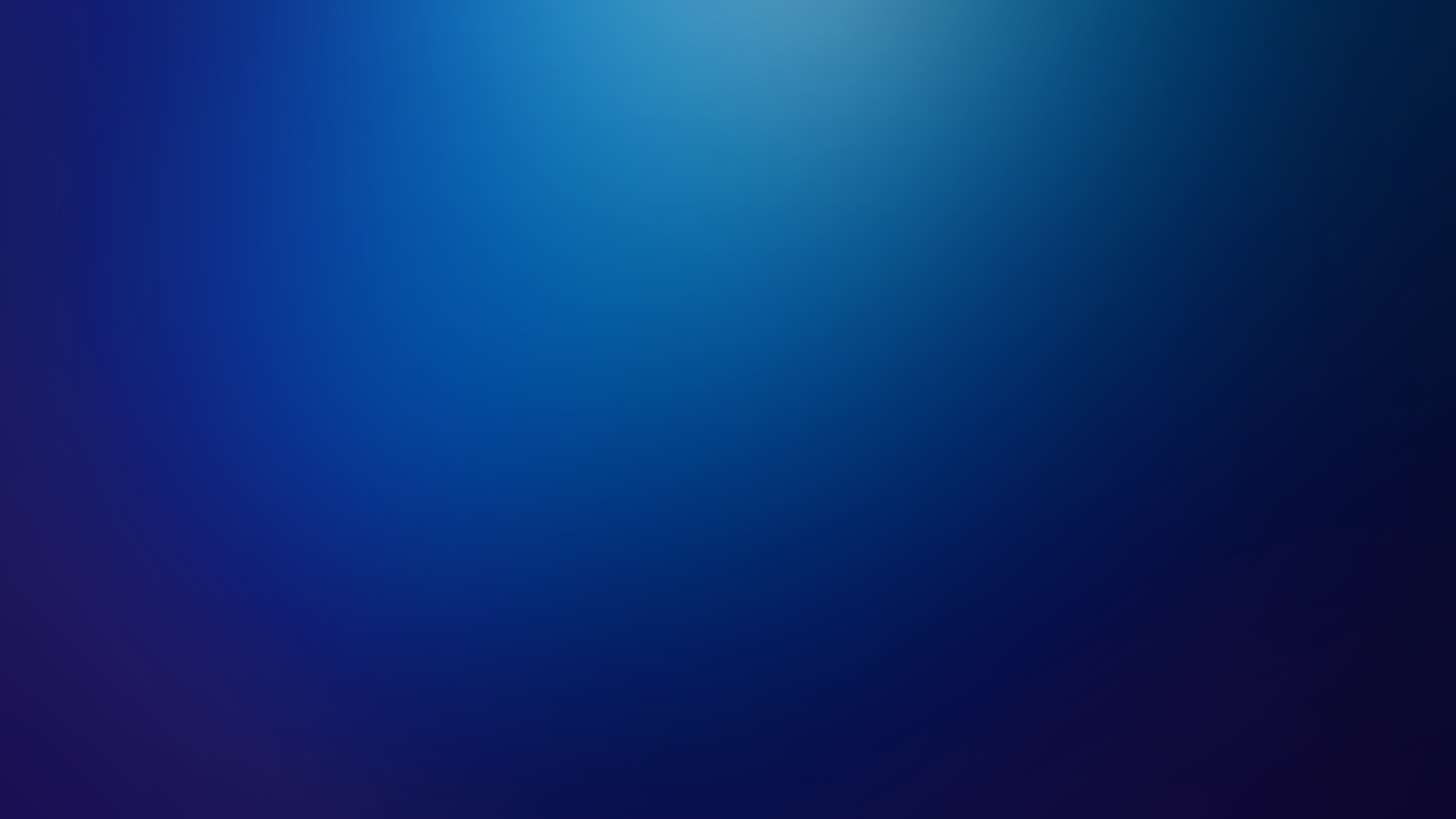
At a Glance
Integrated real-time assessment of gauge, curvature, elevation, alignment, cant, rail wear, surface, and full rail profile
Highly accurate at speeds over 200 mph
Remote control and diagnostics
High reliability and low maintenance
The DMA TGMS has been used in North America since 2013 by Class I railroads and Amtrak, as well as tested on the TTCI high tonnage loop (HTL).
DMA has supplied autonomous systems in, among other countries, the United Kingdom, Germany, Belgium, Netherlands, France, Japan, Malaysia, and Italy, as well as locomotive-mounted autonomous systems in Mexico and Australia.
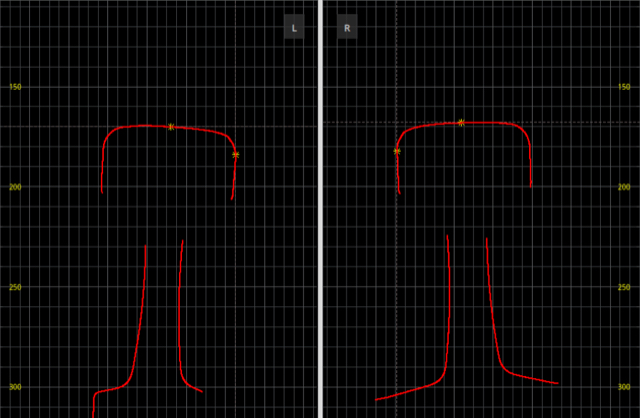
Standard and Upgraded System Descriptions
The standard DMA system is a complete TGMS measuring inner rail profiles. It consists of two measuring units for the gage side of each rail. The measuring units each contain a single laser and two profile sensors for redundancy and enhanced accuracy. The rail geometry beam also contains an inertial pack.
A DMA system enhancement to provide improved rail profile and cant data is available and recommended by Tetra Tech to provide a full rail profile. This upgrade installs a second set of lasers on the field side of the rails in the same beam.
Measurement Principle
The measurement system works by means of lasers and sensors—coupled with an inertial measuring unit (IMU)—to measure the relative position of the track, as described in EN13848-1/2. This European standard meets or exceeds applicable Federal Railroad Administration regulations in Title 49 of the Code of Federal Regulations Part 213, Track Safety Standards. The rail profiles, as shown in the image, are measured to provide the rail reference points and enable the evaluation of wear. The reference points are established in an IMU-referenced coordinate system.
The system uses Class 3B lasers that can collect rail profiles every one-half inch to a maximum frequency of 400 hertz (Hz) for track geometry measurements and to a maximum of 1,000 Hz for turnout and crossing geometry measurements. The lasers are focused and pulsed so they are eye-safe outside the field of view of the rails.
Data Outputs
Data from the TGMS are streamed to the Tetra Tech RailAI Control System, which integrates the data into the telemetry data stream for transmission to the client. Client-defined defects are prioritized for immediate broadcast. Track measurement data in client-specified formats are transmitted continuously, subject to available bandwidth and communications. Improved spatial referencing enables highly accurate positioning for correct application of business rules. This ability to pinpoint the specific track minimizes the need for back-office review, enabling real-time reporting with a low rate of false alarms.